An in-depth guide to screen printing
Share
The craft of screen printing, an age-old method that produces amazing visuals on surfaces ranging from t-shirts and posters to stickers & labels, has been used for centuries by various creators, such as fashion designers and hobbyists.
In this blog, we will explore the evolution of this technique up until modern-day applications through its many years in existence since ancient China. From vibrant colors to intricate designs, all derived from one specific art form.
Takeaways
- Screen printing is an art form with a long history and many applications, including fashion, textiles, artwork & decor.
- It involves creating a design/stencil and transferring ink onto the substrate using mesh screens.
- DIY screen printing can be achieved from home by following step-by-step instructions and researching different techniques.
The art of screen printing
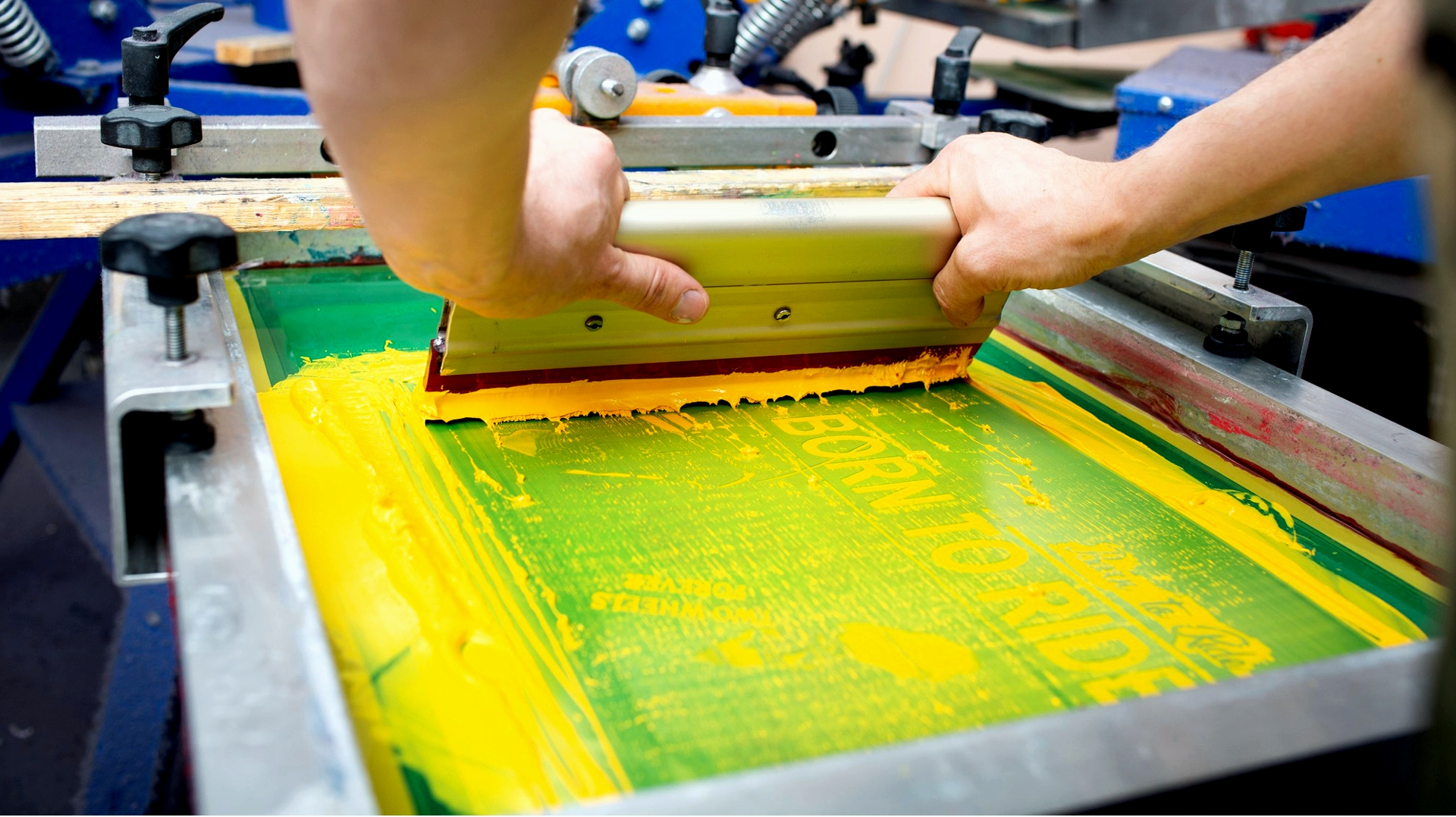
The printing technique known as silk screen or serigraphy, has been employed for over a century and is widely used in different industries around the world. Popularised by artist Andy Warhol, it is particularly favoured in producing fine artworks such as posters. It’s also utilised to create custom garments.
Commercial use on clothing takes up more than half of all silkscreen activity made possible through Michael Vasilantone’s invention - the screen-printing press! Famous artists including Bob Dylan, James McQueen and Billy Connolly have adapted this method into their own works too. The silk screen process involves layering multiple stencil designs onto screens before transferring these prints one layer at a time with ink applied using rollers or squeegees then exposed to heat or light so that each color can be set firmly into place permanently unto fabric material via an appropriate type of printing press depending upon budget restraints etc…
From Ancient China to Modern Pop Art
The technique of screen printing, which goes by the name “silk screen printing” due hence the name due to it using silk as its mesh material back in the Song Dynasty (960-1279 AD) in China, eventually spread throughout Western Europe where it found a new appreciation during the 20th century with pop artists like Andy Warhol and Roy Lichtenstein. They reinvigorated how people viewed this form of industrial application by introducing multiple colors into their prints thus turning what was once seen merely an practical utility tool into respected pieces of modern art.
The Role of Screen Printing in Fashion and Textiles
Screen printing has greatly impacted the fashion and textile industries with its ability to create vibrant, intricate designs on fabrics such as silk. Companies like Biddle Sawyer Silks have been utilizing this technique for over 50 years, primarily via photo emulsion which involves a transparent acetate film.
This process is advantageous in several ways: it offers accuracy with minute detail, enables you to print onto an assortment of fabric varieties, provides versatility thanks to the range of available printing ink types multiple colors that can be used.
Unfortunately one major downside when using screen-printing in fashion or textiles would be meeting minimum order quantities – Around 200m/color – which may not always fit multi-colored design requirements.
The Screen Printing Process Unveiled
Screen printing is a complicated and captivating operation that involves designing, stenciling, crafting of silk mesh screens with ink or emulsion application for transfer onto the desired material. The mesh screen takes center stage during this process as it helps to move the printer’s inks towards its destination while also controlling where they don’t end up going through determination of these areas by means of an established template.
This approach can be utilized via manual presses, semi-automated systems or fully automatic mechanisms relying on what outcome is sought after and how big are scale production demands respectively.
Preparing the Design and Stencil
The essential part of the screen printing process is creating a design, and this can be very simple or elaborate. The actual procedure then proceeds to making a stencil. With photo emulsion being one method used to produce it. This makes up an integral role in determining how the finished printed product looks as its allows for some ink coverage while other parts are blocked out entirely. When it comes to overall printing production, screens play an important role by allowing certain areas where color will come through whereas others remain untouched – hence why utilizing forms such as those from photo emulsion gets incorporated into the practice commercial screen printing does so often.
Creating the Screen and Applying Ink/Emulsion
The process of creating a screen begins with stretching polyester mesh over either metal or wooden frames. After it’s ready, the ink or emulsion is applied across its surface using a tool called a squeegee to spread an even coat along all parts of the frame. Exposing this layer to bright light also allows for hardening and development that will result in forming the stencil while leaving spaces open through which printing can occur later on during said process. These openings offer pathways from where both film-based ink and liquid solutions are able to travel when being used for various forms of printing methods at hand.
Transferring the Design and Printing
The actual process of screen printing begins by placing the mesh onto a chosen surface and securing it with pallet tape. Then, a squeegee is used to press ink through the holes in the netting, transferring that pigment on to whatever board was being printed upon. Once all of this has been accomplished properly - using heat-resistant paint plus accurate drying parameters regarding time and temperature – then you should have an enduringly vibrant image remaining after lifting off said screen carefully so as not to disrupt its outline from beneath. When done correctly following every step required for successful completion in your specific instance ofscreen printing process procedure , you can rely on creating lasting prints adhering precisely how they had originally started out looking!
Screen Printing vs Digital Printing: Pros and Cons
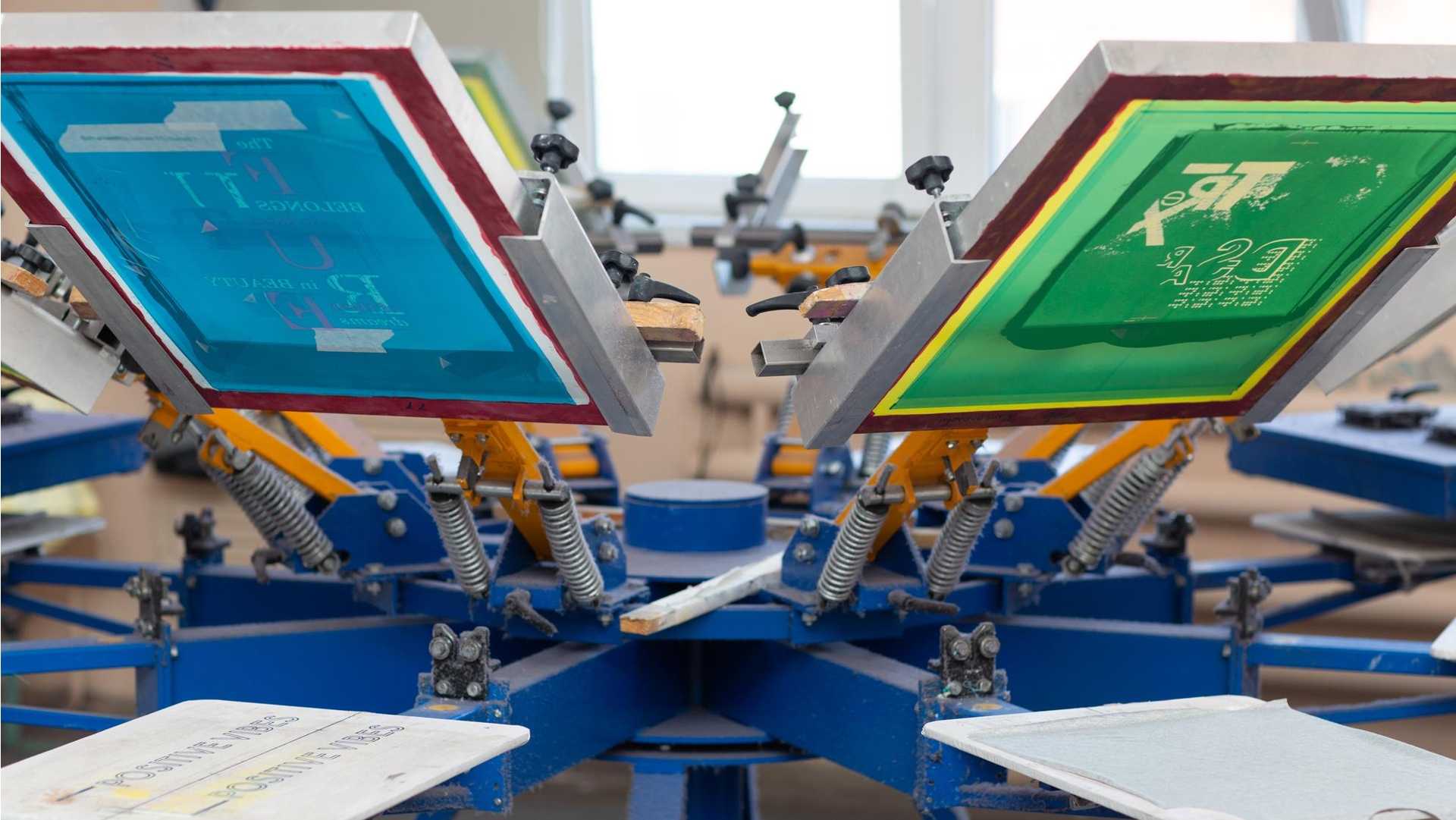
When selecting between a screen printer and digital printing, factors such as intended result, production size and required detail in the finished product must be taken into account. Digital printing can provide intricate designs ideal for lower quantity jobs or individual customizations with its capacity to create detailed graphics. On the other hand, Screen Printing excels at delivering bright colors, making it perfect when a large number of items need producing on various materials. Consequently choosing one method over another depends upon what outcome is desired from the print job.
Advantages of Screen Printing
Screen printing is a go-to choice for many projects due to the quality of color it provides, which often surpasses digital printing. It can also be used efficiently in large batch productions since the printing board a stencil allows replicating designs without any additional effort or cost involved. Its application works with an extensive range of materials making screen printing extremely versatile and desirable overall.
Drawbacks of Screen Printing
Despite the potential advantages, there are some constraints to screen printing. One of these is that you cannot create intricate and detailed designs due to the limitation on colors used in one such printed design. It can be labor-intensive as a result of various stages involved throughout this process which may take up several hours or even days for completion depending on its complexity. This makes screen printing not ideal when looking for prompt turnaround times or smaller production runs.
Non-Textile Applications of Screen Printing
Screen printing is a versatile technique that can be used to produce artwork, stickers and labels on all kinds of materials such as glass, ceramics, wood and paper. This form of printmaking has become invaluable across several industries due to its ability to create stunning designs using various substrates with precision accuracy. The use for screen printing does not stop at textiles. It also extends into the making home decorations Other products including electronics etc.
Screen Printing Stickers & Labels
Screen printing is a process utilized to craft top-notch stickers and labels for many different products and businesses. The procedure starts with designing the desired artwork, which then has to be transferred onto a mesh screen printer using film positive. After that, emulsion must be applied on it before setting up the prepared 230-mesh screen ready for use. Combining solvent ink along with this particular type of equipments produces an outstanding final product, colorful tags or labels of superior quality finish are created in no time!
Screen Printing in Art and Decor
Screen printing is an oft used technique by artists, with which they can craft unique artworks for displays and decorations. To carry out the process of screen print art requires a series of steps: conceiving the image to be printed, designing stencils that conform to mesh size of this envisioned work, using emulsion in covering up the selected surface or ‘screen’, putting together pieces from these templates onto said area covered beforehand, laying down ink on top level so as it doesn’t spread beyond expected areas when being pushed forward through vigorous application of a squeegee tool - concluding with a striking print embodying its creator’s vivid imagination and skilful manipulation of one technology. Each piece produced will feature prints marvellous enough entice all kinds onlookers!
DIY Screen Printing: A Beginner's Guide
DIY screen printing gives you the opportunity to tap into your creativity and customize items with unique designs. It doesn’t matter if it’s t-shirts, other artwork or simply a new hobby, these projects can be highly enjoyable while resulting in results that look professional. With some practice using the right tools and materials, home is where high quality print jobs will happen! Not only does DIY screen printing open up possibilities for personalization of products but also provides endless potential when it comes to creative expression.
Essential Materials and Tools
Printing at home can be done with the right materials and tools, such as a mesh screen (like aluminum, polyester or nylon), squeegee (rubber, plastic or metal) , ink plus stencil supplies. To ensure success of your printing project it is recommended to acquire all necessary items through an introductory kit available on the market, these usually have everything you need for beginning this process. Alternatively inks and different types of stencil materials may also be purchased separately according to individual preferences.
Tips for Successful Home Screen Printing
Delving into the realm of DIY screen printing takes practice and determination for successful results. Begin with practicing on objects such as scrap fabric or paper to develop your skills prior to starting a project. Remember that the ink needs adequate drying times, usually 24 hours, in order for it to be effective. Consider researching various techniques while following instructions step by step so you can find which is most beneficial to you!
With dedication and perseverance ,you will soon achieve the possess printed creations demonstrating your inventiveness and capabilities .
Summary
Screen printing is a highly detailed process with an illustrious past, beginning in old China and extending to current art, fashion trends, and industries. Appreciated for its vibrancy of colors as well as the intricacy achievable through designs, this method has gained steady popularity amongst both professional artists or home crafters alike. For anyone starting out on their screen-printing journey remember that continual practice plus perseverance are essential keys to success. By having all necessary materials at hand along with acquired techniques you’ll be able creating dazzling customized pieces easily reflecting your creative flair! So let’s get started today – happy printing!
Frequently Asked Questions
How do you do screen printing?
Screen printing entails making a stencil of the image that is to be printed, where certain parts of printed image are hardened and others remain soft. After removing the film, any soft regions can then be washed away using water and ink applied with a squeegee onto the screen before transferring it all over to whatever material will bear its print.
Which is better screen printing or sublimation?
When it comes to large-scale production, the screen printing method offers the best results on cotton fabrics. It can take more time but sublimation produces brighter and livelier hues for materials like polyester blends that consist of high amounts of synthetic fibers as well as light-colored fabric with a polymer coating.
What is the main difference between screen printing and digital printing?
Printing by screen involves the use of a stencil to move ink onto the material being printed, whereas digital printing eliminates separate stencil for this step and goes straight from applying ink directly on to what’s getting printed.
What are some non-textile applications of screen printing?
Screen printing is a productive approach for producing items like labels, artwork, stickers and home decor that can withstand the test of time. This technique is also utilized in numerous industries to craft economical outputs with great durability.